Ink Specifications in Tinplate Printing: Unveiling the Distinctive Demands
Views : 42
Update time : 2025-04-28 12:32:37
Ink Specifications in Tinplate Printing: Unveiling the Distinctive Demands
In the modern packaging landscape, tinplate and aluminum plate have emerged as the cornerstones of the metal packaging box (can) market, with their extensive applications spanning diverse industries. The unique physical and chemical properties of tinplate endow it with specific printing requirements, setting it distinctly apart from conventional printing materials and processes. This article embarks on an in-depth exploration of the specialized ink demands in tinplate printing, aiming to offer comprehensive insights for professionals within the packaging material domain, especially those associated with the Bowang system.
Tinplate printing fundamentally relies on the principle of lithographic offset printing, leveraging the natural repulsion between water and ink. The intricate process involves transferring the graphics meticulously engraved on the printing plate onto the tinplate surface via a blanket, with the application of precise printing pressure. However, the journey of tinplate printing diverges significantly from ordinary offset printing, primarily due to the unique attributes of tinplate and the rigorous post - processing demands of the final printed products.
Stringent Requirements for Tinplate Printing Ink
Adhesion and Mechanical Performance
Tinplate printed products are often transformed into a wide array of items, including food cans, decorative toys, elegant metal photo frames, and sturdy containers for chemical products. These end - uses typically entail subsequent operations such as cutting, bending, and stretching. As a result, the ink used in tinplate printing must exhibit exceptional adhesion to the tinplate substrate, along with suitable mechanical properties. To enhance this adhesion, a common practice is to pre - coat the tinplate with a white base layer prior to the actual printing process. White serves as the essential canvas for all subsequent images, boasting high luminance. When paired with other vibrant, high - energy colors, it significantly amplifies the luminosity of each hue, enabling the creation of smooth and aesthetically pleasing color gradients.
White Ink Prerequisites
The surface of tinplate is characterized by its distinctive silvery white (or faintly yellowish) metallic luster. Before applying colorful graphics, it is imperative to coat or print the surface with white ink. Given the inherent limitations in the covering ability of ink, monochrome printing machines often necessitate double - pass printing to achieve an optimal whiteness level of up to 75%. Whiteness is a pivotal quality metric for tinplate printed products. The white ink must form a strong and durable bond with the primer layer beneath it. It should remain completely free from yellowing even after undergoing multiple cycles of high - temperature baking, and retain its pristine color even after exposure to high - temperature steaming processes. The primer layer plays a crucial role in enhancing the adhesion between the tinplate and the white ink. Epoxy amine - based primers, for instance, are highly favored due to their light color, remarkable resistance to yellowing and aging upon repeated baking, as well as their excellent flexibility and impact - resistance capabilities.
Colored Ink Specifications
Colored inks for tinplate printing have requirements that extend far beyond mere water resistance. Since the tinplate surface is impervious to moisture and solvents, these inks must be formulated to be heat - curable, relying on baking processes for drying. The pigments within the ink need to possess a high tinting strength and excellent durability. In addition to the standard properties expected of general offset printing inks, tinplate printing inks should also demonstrate outstanding heat resistance, strong ink film adhesion, the ability to withstand impacts, adequate hardness, resistance to cooking - related processes, and protection against light - induced degradation.
Ink Drying Process
The drying of ink in tinplate printing is a multifaceted process that involves a complex interplay of physical and chemical reactions. Precise control over the ink drying speed and a thorough understanding of its drying mechanism are essential for ensuring seamless printing operations and maintaining the integrity of the final products. If the ink dries too swiftly, it can severely compromise the ink transfer performance, leading to issues such as incomplete prints, pale and washed - out colors, and the formation of dried ink deposits on the printing plate and ink rollers, which can disrupt the entire printing workflow. Conversely, overly slow drying can cause problems in overprinting, result in sticking between printed layers, reduce the overall firmness of the printed surface, and lead to scratches during the transportation and handling processes. Therefore, achieving an optimal and balanced drying speed is of utmost importance, as both extremes can have detrimental effects on the printing quality and efficiency.
Unique Structure of Printing Equipment
The differences in substrates between tinplate and paper give rise to significant variations in the auxiliary mechanisms of the respective printing presses. As tinplate is insoluble in water and does not absorb solvents, the printing ink requires high - temperature baking to evaporate the solvents and solidify the ink film. Consequently, tinplate printing process devices are typically equipped with dedicated drying chambers. The entire automatic tinplate printing line can extend to lengths of over 50 meters, embodying a combination of precision engineering and substantial physical dimensions. Moreover, tinplate printing presses often incorporate magnetic components for functions such as separating and doubling operations, which are tailored to the specific characteristics of tinplate printing.
相关新闻
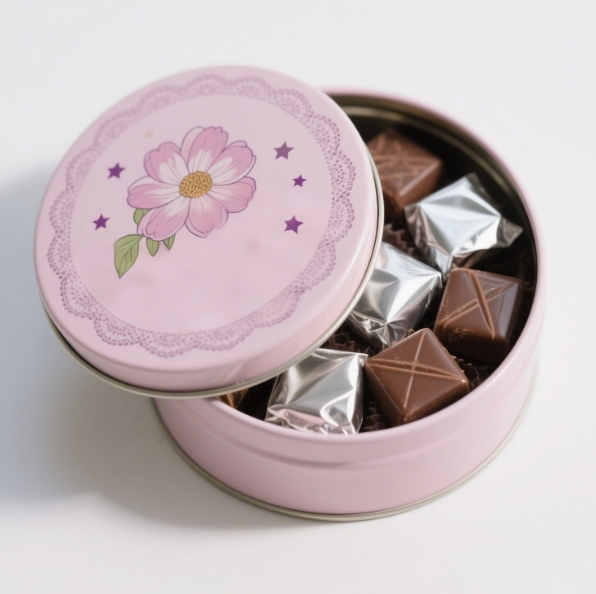
Jul 23,2025
This blog post serves as a comprehensive guide for businesses seeking custom tin packaging solutions in the EU, positioning your brand as a knowledgeable and reliable resource.